2025年4月3日,上海交通大学核科学与工程学院核工程材料实验室与中国核动力研究设计院核反应堆技术国家重点实验室,在国际期刊《Corrosion Science》上发表了题为“Revealing the mechanism of corrosion products deposition in Cr-coated fuel cladding”的研究论文。
在模拟压水堆一回路环境下,使用内加热回路系统,对比研究Cr涂层包壳及锆合金包壳表面的腐蚀产物沉积行为,系统揭示了Cr涂层包壳腐蚀产物的微观结构和沉积机制,为Cr涂层包壳材料的工程应用与服役预测提供了重要数据支撑。 上海交通大学为该论文的第一完成单位,博士生黄涛为该论文的第一作者,上海交通大学张乐福研究员、陈凯副教授及中国核动力研究设计院庞华研究员为论文的共同通讯作者。
一回路冷却剂中的腐蚀产物在包壳表面发生沸腾沉积,简称CRUD,对反应堆的长期高效运行构成了巨大挑战。CRUD层降低了包壳传热系数,导致温度升高,可能诱发局部腐蚀破损,另一方面,多孔的CRUD会从冷却剂中捕获硼,导致功率轴向偏移。近年来,Cr涂层锆合金由于其出色的耐腐蚀性能,成为备受关注的新型包壳。然而,多数关于Cr涂层的研究都集中在事故工况下,对其腐蚀产物沉积行为的研究存在空白。 CRUD 的形成受到众多因素的影响,涵盖腐蚀产物的化学性质、沸腾状态以及表面特性。Cr涂层表面与传统锆合金表面在化学特性、腐蚀(溶解)行为等方面存在明显差异,对CRUD成分和沉积机制有明显影响。该团队最近的研究成果发现水化学环境中的微量溶解氧会诱发Cr涂层迅速溶解。溶解释放的HCrO4-可作为腐蚀产物源项,参与复杂的CRUD形成过程,目前尚无相关深入研究。因此,厘清Cr涂层表面腐蚀产物的沉积行为机制对于全面评估Cr涂层的可行性和长期服役性能至关重要。 材料制备与测试 为模拟核反应堆复杂的高温高压流动环境,本研究搭建了如图1所示的内加热腐蚀产物沉积环路测试系统,以维持测试段入口恒定的高温、高压、高流速条件。测试段内同时放置了Cr涂层和无涂层的锆合金样品,通过直流加热棒使包壳表面处于过冷核沸腾状态。通过混合高纯氩气和氧气将溶解氧水平控制在 300±10 ppb。腐蚀产物通过亚铁乙酸和乙酸镍溶液被引入回路系统中,维持Fe和镍Ni浓度分别为 45±5 ppb和 35±5 ppb。研究中连续进行了 2000 小时的长期积垢测试,确保接近堆芯的沉积条件,最后结合 SEM、TEM、XRD、EDS 等多尺度表征手段,系统解析了CRUD的微观结构与沉积演化规律。 图1 腐蚀产物沉积测试系统示意图 不同质量蒸发率下的CRUD厚度如图2所示。积垢层厚度随着蒸发率增大而提高。Cr涂层表面CRUD厚度明显大于锆合金。通过FIB-SEM分析区分了CRUD钟的致密层与疏松层,在蒸发率较高的样品中致密层较为显著,而多孔层在所有样品中都保持相对稳定,厚度约为4~6微米。 高蒸发率下 CRUD 的截面SEM和EDS分析结果如图3所示。Cr涂层和无涂层的锆合金表面均呈现出双层CRUD结构,包括多孔的外层和致密的内层。外层多孔层主要由Fe、Cr、Ni氧化物组成,Fe 是主要元素;而致密内层缺乏Ni,由Cr 和Fe的混合氧化物相组成。 图 2 Cr涂层和无涂层锆合金表面的CRUD厚度与质量蒸发率的关系 图 3 高蒸发速率下的横截面 FIB-SEM 和 EDS 分析:(a-c)Cr-30 样品;(d-f)Zr-30 样品;(g-i)高倍观察 如图4所示,中等蒸发率下,Cr涂层和无涂层锆合金样品的CRUD总体结构保持一致,各层厚度存在差异。图5展示了低蒸发速率下Cr涂层锆合金和无涂层锆合金上形成的CRUD 的截面分析结果,与中高蒸发速率不同的是,低蒸发速率样品表面均呈现出单层多孔 CRUD 结构。 图 4 中等蒸发率下的FIB-SEM 分析:(a)Cr-25 样品,(b)Cr-20 样品,(c)Zr-25 样品,(d)Zr-20 样品以及(e)、(f)能谱分析 图 5 低蒸发率下的FIB-SEM 和 EDS 分析:(a-c)Cr-15 样品,(d-f)Zr-15 样品 图 6 展示了沉积测试后样品的 XRD 图谱,揭示了存在显著的尖晶石相、基体相(Cr/Zr)以及α-CrOOH 相。 图 6 腐蚀沉积后所有样品的X射线衍射图谱:(a)Cr涂层和(b)无涂层Zr合金 TEM分析表明多孔层主要由直径约为 50nm的Fe,Ni,Cr尖晶石氧化物的纳米颗粒组成,而致密层则由CrOOH和Fe2O3等块状混合物构成(图7)。图8对Fe,Cr,Ni三相混合氧化物进行热力学分析表明,在pH接近中性时,CrOOH、NiFe₂O₄ 是稳定的相,而在酸性或高电位环境中,Fe₂O₃ 占主导地位,这表明NiFe₂O₄ 在热力学上比 NiCr₂O₄ 更稳定。NiFe₂O₄与NiCr₂O₄的混溶性分析表明,320℃下,Cr在NiFe₂O₄中的最高溶解度为0.2左右,与TEM-EDS分析得到的Ni(Fe₁.₆Cr₀.₄)O₄高度吻合。 图 7 表层 CRUD 的TEM分析:(a-b) HAADF和DF图,(c)TKD分析,(d)CRUD 顶部放大图(e-h)能谱分布图,(i)纳米颗粒簇放大图以及(j)能谱图,(k)纳米颗粒的HRTEM图以及相应的(l)FFT花样,(m)多孔层与致密下层界面,(n-p)致密层内各种物相的SADE花样 图 8 CRUD 组分的热力学分析:(a)Fe-Cr-Ni 系统中的 Cr,(b)Fe-Cr-Ni 系统中的 Fe,(c)Fe-Cr-Ni 系统中的 Ni 以及(d)NiFe₂O₄-NiCr₂O₄尖晶石二元系的不混溶性 图9总结了Cr涂层表面和无涂层Zr合金表面CRUD的形成机制,引入溶解氧后,在 Cr 涂层表面,Cr 溶解和腐蚀产物沉积同时发生;而在 Zr 表面,只有腐蚀产物沉积。溶解产生的Cr(VI)在包壳管表面被还原为Cr(III)后优先进入NiFe₂O₄尖晶石中,而在超出溶解极限Ni(Fe₁.₆Cr₀.₄)O₄后以CrOOH的形式沉积,形成底部的致密层。 图 9 Cr涂层和无涂层锆合金的CRUD行为示意图:(a-c)分别为Cr涂层锆合金在低、中、高蒸发速率下的积垢行为,(d-f)无涂层锆合金在对应工况下的积垢行为
通过搭建内加热腐蚀产物沉积环路测试系统,对Cr涂层与无涂层锆合金包壳在模拟堆芯工况下的腐蚀沉积特性展开对比实验,结合微观表征揭示了Cr涂层包壳在微量溶氧环境下的腐蚀产物沉积机制。主要发现如下: 1.Cr涂层表面的沉积层厚度高于无涂层样品,这主要是由于Cr溶解导致富Cr的腐蚀产物在涂层表面大量沉积。 2.蒸发速率在沉积层的结构和厚度演变中起到关键作用:低蒸发下形成以Ni(Fe₁.₆Cr₀.₄)O₄纳米颗粒为主的多孔沉积层;随蒸发率提高,多孔层下方生成由CrOOH基质与Fe₂O₃晶块构成的致密层,其厚度与随蒸发速率呈正相关。 3.典型的腐蚀产物NiFe₂O₄主要通过颗粒吸附沉积在包壳表面,而Cr涂层溶解产生的Cr(VI)通过还原饱和结晶机制进行沉积。冷却剂中的Cr(VI)在沸腾表面被还原为Cr(III)后以过饱和结晶的形式发生再沉积。
免责声明:本网站所转载的文字、图片与视频资料版权归原创作者所有,如果涉及侵权,请第一时间联系本网删除。
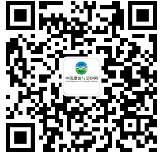
官方微信
《腐蚀与防护网电子期刊》征订启事
- 投稿联系:编辑部
- 电话:010-62316606
- 邮箱:fsfhzy666@163.com
- 腐蚀与防护网官方QQ群:140808414