磨损的过程 机械零件的使用寿命在很大程度上取决于零件的耐磨性。在摩擦副的材料、热处理情况和润滑条件条件确定的情况下,零件的表面质量就起着决定性的作用。 零件的磨损过程通常分为三个阶段。 I :初期磨损阶段,也称为磨合阶段。当两个零件表面刚开始接触时,只是表面粗糙的凸峰相互接触,实际接触面积很小,单位面积压力很大,不能形成润滑油膜,接触处形成局部干摩擦,其应力可能超过金属的屈服极限和强度极限。随着摩擦副的相对运动,接触部分金属被撕裂、破碎或切断,凸峰很快被碾平,磨损速度较快。 II :正常磨损阶段。随着磨合过程的进行,表面粗糙度值逐渐减小,实际接触面积增大,单位面积压力减小,摩擦表面之间具有良好的润滑条件,磨损将以缓慢速度进行。 III :急剧磨损阶段。经过相当长一段时间后,随着磨损的进行,表面粗糙度值继续减小,润滑油被挤出接触面,致使接触面间形成了半干摩擦,甚至干摩擦,摩擦阻力增大,加剧了表面磨损。同时,由于实际接触面积进一步增大,促使接触表面间分子吸附力增大,从而容易出现表面分子粘合的表面咬焊现象,随着运动的进行,局部咬焊的表面将被撕裂。有时还会由于摩擦产生的大量热量,使接触表面出现高温,改变金属组织,降低表面硬度,甚至还能使局部接触表面熔焊在一起,导致磨损剧烈增加。 表面粗糙度对耐磨性的影响 零件初期磨损量与表面粗糙度值有着密切的关系。在一定工作条件下,都存在一个初期磨损量最小的最佳表面粗糙度值。一般工作情况,表面粗糙度Ra值为0.4μm~0.8μm时,初期磨损量最小。 表面轮廓对耐磨性的影响 表面轮廓形状对零件的耐磨性也有显著的影响。在相同粗糙度下,以下6种由于表面轮廓形状的差异,使零件间的实际接触面积和润滑油的存留情况变化很大,零件的耐磨性相差甚远。 (b)、(d)、(f)轮廓形状表面将比同组的(a)、(c)、(e)轮廓形状表面耐磨。 表面纹理方向对耐磨性的影响
零件表面的加工纹理方向与相对运动方向的相互关系,对磨损量也有很大影响。
在轻载时,纹理方向与相对运动方向相同时磨损量最小,相垂直时磨损量最大。在重载时,当两表面纹理相垂直,且运动方向平行于下表面的纹理方向时,磨损量最小;当两表面纹理方向与运动方向相同时,容易发生咬合,磨损量最大。
机械加工后的零件经冷态塑性变形,表面的显微硬度都有所增加,从而减小了表面进一步塑性变形和表面层金属咬焊的可能,提高了耐磨性。
但加工硬化到一定程度后,如再进一步冷作硬化,将会引起金属组织的过度“疏松”,使磨损加剧,甚至出现裂纹与剥落,反而使耐磨性能下降。
下图为T7A碳素工具钢,当其表面显微硬度提高到380HB时,其耐磨性达到最佳值,如显微硬度进一步提高,其耐磨性反而会下降。
免责声明:本网站所转载的文字、图片与视频资料版权归原创作者所有,如果涉及侵权,请第一时间联系本网删除。
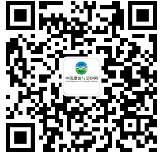
官方微信
《腐蚀与防护网电子期刊》征订启事
- 投稿联系:编辑部
- 电话:010-62316606
- 邮箱:fsfhzy666@163.com
- 腐蚀与防护网官方QQ群:140808414